What is the final inspection
Final inspection is a quality control process that occurs after
production is completed but before products are shipped to customers or distributors.
Final inspection is a comprehensive examination of finished products to verify that they meet all specified quality standards, functional requirements,
and customer expectations. It serves as the last quality checkpoint before goods leave the manufacturing facility or warehouse for delivery.
This last check helps catch any overlooked defects, verifies proper packaging, and confirms that products are ready for delivery to customers.
Final inspection is conducted after production and before shipment
and it covers finished products in their final packaging.
To ensure overall product quality and compliance our experts at AQM BD use visual checks, functional tests, and measurements.
It helps determine whether products are approved for shipment or require rework.
This process aims to catch any defects or issues that may have been missed during earlier production stages, helping to maintain product quality and customer
satisfaction.
“AQM BD's final inspection Final inspection is a quality control process performed on finished products just before shipment. It involves a thorough examination to ensure that goods meet all quality standards, specifications, and customer requirements.”
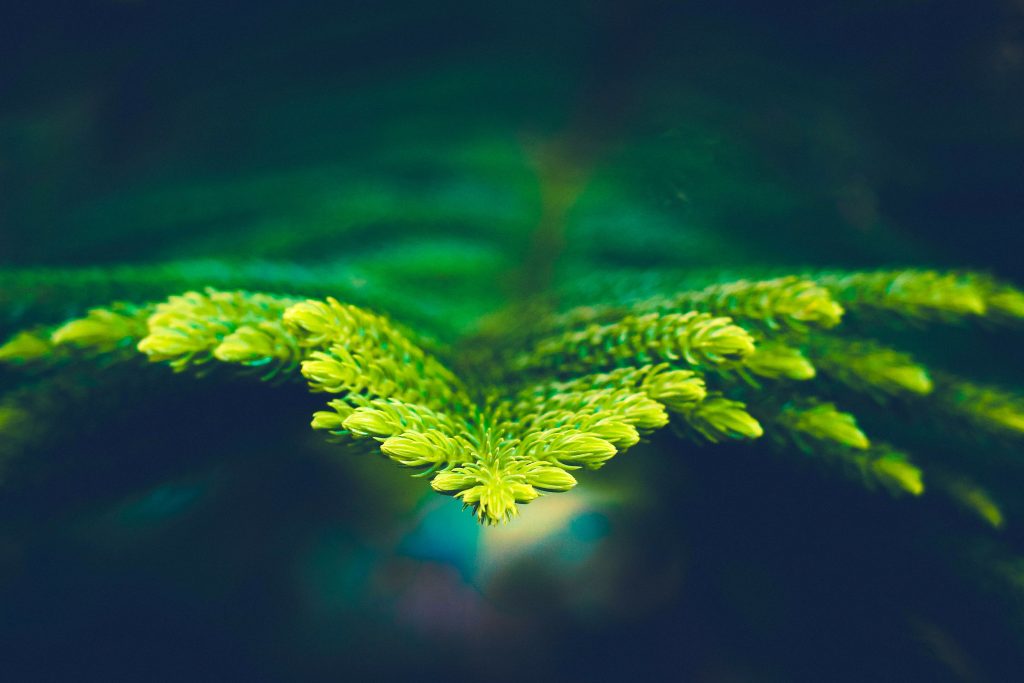
Benefits of the final inspection
Tcontributes to a comprehensive final inspection process, ensuring that only products meeting all necessary criteria are shipped to customers.
The specific implementation may vary depending on the product type, industry standards.
The final Inspection ensures products meet specified quality standards, verifies consistency across production batches, catches issues before products reach customers and
reduces the risk of shipping defective items.
It also helps deliver products that meet or exceed expectations and minimizes customer complaints and product returns
Decreases customer service issues related to product quality.
It also prevents expenses associated with recalls or returns and reduces long-term costs by identifying systemic issues.
Key methods used for the final Inspection:
- Visual Inspection: Examining products for visible defects or cosmetic issues
- Functionality Testing: Verifying that products work as intended and testing all features
- Measurements and Tolerances: Checking dimensions against specifications and ensuring products fall within acceptable tolerance ranges
- Packaging Examination: Inspecting packaging integrity and quality and verifying correct packaging materials and methods
- Labeling and Documentation Check: Ensuring accurate and complete product labeling
- Packaging Examination: Inspecting packaging integrity and quality.
Sourcing Inspection
Sourcing inspection is a quality control process where products or materials are examined at the supplier's location before shipment to the buyer.
find out more
Sourcing Inspection
Reduces the risk of receiving non-compliant items. This inspection occurs during or after production but before the goods leave the supplier's facility, helping to catch quality issues at the source.
Inline Inspection
Examining products or components during the production process, rather than after completion.
find out more
Inline Inspection
Detecting defects or issues early, allowing for immediate correction and reducing waste.
Final Inspection
Final inspection is a quality control process conducted after production is complete but before goods are shipped to the customer.
find out more
Final Inspection
It involves a thorough examination of quality standards, cosmetic requirements, and functional specifications. This last check helps catch any defects that may have been missed during production.
Loading Inspection
Loading inspection is a quality control process performed during the loading of goods onto transport vehicles for shipment.
find out more
Loading Inspection
Prevents shipping errors, damage during transit, and ensures that the right products in the right condition are dispatched to customers or distributors.