Quality inspection and technology
Quality inspection is increasingly leveraging advanced technologies to enhance accuracy, efficiency, and coverage. Artificial Intelligence (AI) and Machine Learning (ML)
algorithms are being employed to detect defects that might be missed by human inspectors.
These systems can analyze thousands of product images in seconds, identifying
subtle irregularities or deviations from quality standards.
Internet of Things (IoT) devices are also being integrated into
production lines for real-time quality monitoring.
Sensors can track various parameters such as temperature, humidity, and production speed, alerting managers to potential quality
issues before they escalate. This proactive approach helps in maintaining consistent quality throughout the production process.
Blockchain technology is being explored for its potential to bring
unprecedented transparency to supply chains.
By creating an immutable record of each step in the production and inspection process, blockchain can help in tracing the
origin of quality issues and ensuring the authenticity of inspection reports.
There's a growing emphasis on sustainability in both sourcing and quality inspection activities. This goes beyond just checking the final product quality to examining the
entire production process for environmental impact.
The multifaceted nature of quality inspection
Inspectors are now often required to verify the use of eco-friendly
materials, assess energy efficiency in production processes, and check compliance with environmental regulations.
This might involve verifying the authenticity of organic
certifications, checking the implementation of water conservation measures, or assessing waste management practices.
In sourcing, there's an increasing preference for suppliers who
demonstrate commitment to sustainable practices.
This includes those who use renewable energy, practice responsible resource management, and have clear policies for
reducing their carbon footprint. The quality of a product is now often judged not just by its physical attributes, but also by the sustainability of its production
process.
Supply chain diversification has become a key strategy, particularly in light of recent global disruptions. Companies are moving away from over-reliance on single sources
or regions, instead developing multiple supplier relationships across different geographical areas.
This approach requires more complex coordination in quality inspection
processes to ensure consistency across diverse suppliers.
Financial health assessments of suppliers have become an integral part
of the sourcing process. This involves analyzing financial statements, credit ratings, and market positioning to gauge the long-term viability of suppliers.
A
supplier's financial instability could lead to quality compromises or supply disruptions, making this assessment crucial.
Below are some key insights into quality inspection and sourcing activities:
- Emphasis on Sustainability: Growing focus on eco-friendly materials and processes
- Risk Management: Greater emphasis on supply chain diversification
- Globalization Challenges: Navigating complex international trade regulations
- Data-Driven Decision Making: Utilization of big data analytics for supplier performance
- Customization and Flexibility: Tailoring inspection criteria to specific product requirements
- Speed to Market: Streamlining inspection processes to reduce lead times
- Cost Pressures: Balancing quality requirements with cost constraints
- Data-Driven Decision Making: Utilization of big data analytics for supplier performance
Rising up to challenges
Cultural differences in business practices add another layer of
complexity. What might be considered a standard quality control process in one country could be viewed differently in another.
For instance, the approach to giving and
receiving feedback, the importance placed on hierarchy, or the concept of timeliness can vary significantly across cultures.
Successful quality inspection and sourcing in
a global context requires cultural intelligence and adaptability.
Adapting to regional quality standards and expectations is crucial. Different markets may have varying perceptions of what constitutes acceptable quality.
For example,
tolerance for minor cosmetic defects might be higher in some markets than others.
Quality inspectors need to be aware of these nuances and adjust their criteria
accordingly. Similarly, sourcing professionals must understand these regional differences to select suppliers capable of meeting market-specific quality expectations.
How to perform a factory audit
Systematic evaluation of a manufacturing facility to assess its operations, capabilities, and compliance with various standards.
find out more
How to perform a factory audit
On-site inspection of a manufacturing facility to assess its production capabilities, quality control processes, working conditions, and compliance with customer-specific standards.
Quality Checking
Examining products, services, or processes to ensure they meet specified standards and requirements.
find out more
Quality Checking
Critical component of quality control that involves the inspection, measurement, and testing of a product, service, or process to verify its conformance to predetermined quality standards, specifications, and customer expectations
Acceptance Quality Level
Fundamental concept in quality control in the context of product inspections.
find out more
Acceptance Quality Level
A statistical tool that defines the maximum number of defective units, considered acceptable during random sampling inspection, per batch.
Recommanded AQL per Industry
AQL compliance with wide range of industry standards and regulations.
find out more
Recommanded AQL per Industry
AQL values can vary significantly across different industries due to the nature of products, regulatory requirements, and customer expectations.
Resources
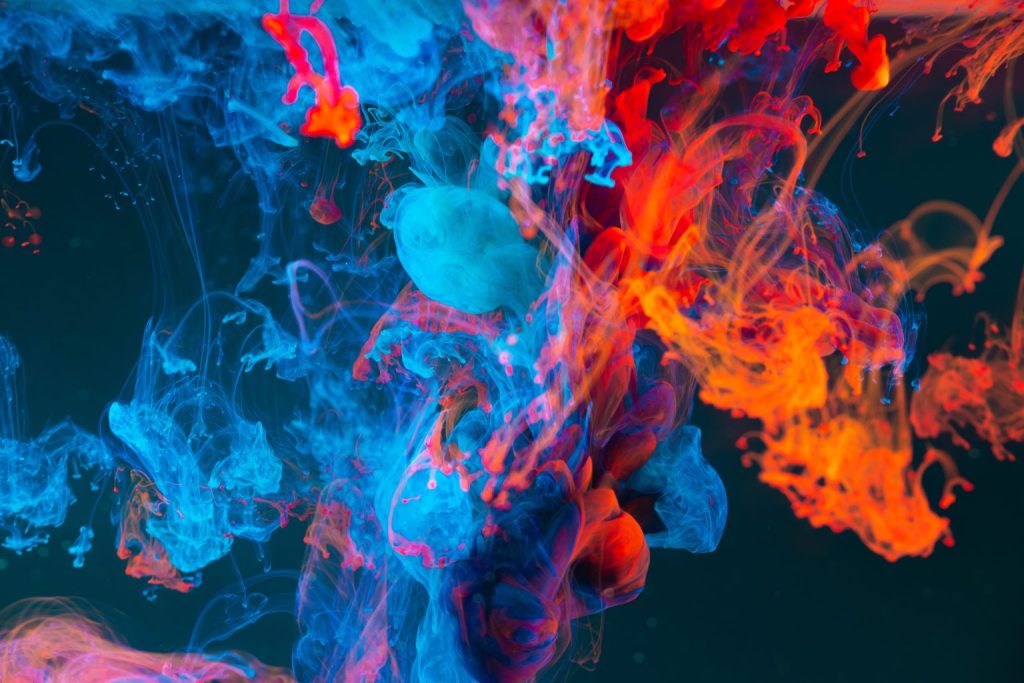
Other services
Inline Inspection
Real-time information about the progress and condition of the manufacturing process during quality checks.
Click Here
Inline Inspection
Get a snapshot of the current state of production at the time of inspection, including progress, issues, and performance metrics.
Loading Inspection
Quality control conducted during the loading of goods onto transport vehicles for shipment.
Click Here
Loading Inspection
Final check performed as products are being loaded for transport, ensuring that the right items in the correct quantity and condition are shipped to customers.